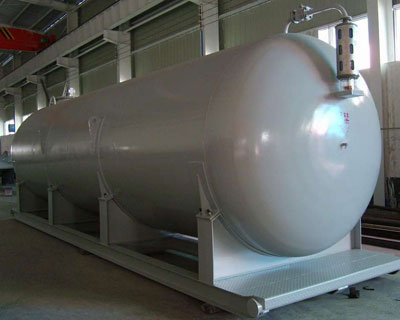 压力容器需要振动时效消除残余应力
在溶剂罐等压力容器制造过程中会产生焊接残余应力。焊接残余应力的存在将影响容器的疲劳寿命,增加其脆性破坏的可能性,同时使抗应力腐蚀的能力减小。为了消除残余应力等不利因素,在焊接后消除残余应力是压力容器制造过程中质量控制的一个重要环节。根据不同材质、板厚及压力容器使用性能要求可能会采取不同方式,其中振动时效无疑是最有效最经济环保的一种。
根据山东华云多年的研究和实践结果,振动时效对金属焊缝及热影响区材料的力学性能基本没有影响。而且由于振动时效降低和均化了残余应力从而使焊缝材料的断裂韧度和疲劳极限明显提高,同时还提高了金属构件的抗应力腐蚀能力。在疲劳极限的提高上振动时效要优于热处理。
早在五六十年代, 国内一些厂家在压力容器制造中就已采用机械法消除残余应力。如对多层高压容器的厚壁筒节环焊缝进行焊接时,焊接工艺规定,每焊完一遍均要用风把对焊缝进行振动敲击,以调整残余应力。在焊接工艺中,为了减少焊接裂纹,往往增加敲击的内容,这些都是用机械法调整焊接残余应力的实例。
哈尔滨焊接研究所和沈阳蒸压釜制造厂对生产的压力容器蒸压釜部件及整体采用振动时效处理,消除焊缝区应力40%以上。 济南第一机床厂为山东齐鲁石化公司储运厂生产的2 500 m3液碱罐, 做了振动时效处理,消除应力30%左右,达到了设计要求。湖北省1台200 m3液化石油气球罐,安装组焊后,采用振动法消除焊接应力 10%~29%,平均约为15%。
虽然国内一些单位对压力容器已有用振动时效代替热处理的实例, 但是由于压力容器是有爆炸危险的特种设备, 国内外压力容器制造法规和标准中均有要进行热处理的明确规定。笔者认为,振动时效作为一项新技术,要在压力容器制造中代替成熟的热处理工艺,必须通过试验获取大量的测试数据,充分地证实其可行性,并通过技术鉴定,且经逐步推广和使用实践,最后才能形成用于压力容器的标准。 |