对切割机的底座应用频谱谐波技术进行振动时效处理,并采用金属磁记忆应力检测法测试了工件振动时效前后的残余应力。结果表明,频谱谐波振动时效技术能够有效降低并均化底座的残余应力,可广泛用于大型铸件残余应力的消除。
振动时效又称VSR(Vibration Stress Relief)振动消除应力法,20世纪70年代引入我国。其实质是在试件的高残余应力区,激振动应力与试样中残余应力叠加,使金属晶体产生位错运动,内部产生微观塑性变形,高残余应力得以释放,达到调整和均化残余应力的目的。应用实例证明,振动时效对稳定构件的尺寸精度具有良好的作用。振动时效技术不仅具有工艺简单、效率高、能耗低等优点,而且克服了某些热处理工艺带来的表面氧化、脱碳、热变形等问题,从而弥补了自然时效和热时效的不足,因此,振动时效技术在机床、航空、航天、汽车、发电设备、冶金、核电站等各制造领域得到广泛应用[1,2]。本文采用频谱谐波技术对切割机的底座实施了振动时效处理,对频谱谐波技术在消除大型铸件残余应力的可行性进行了验证。
1频谱谐波振动时效技术
频谱谐波振动时效技术是通过傅里叶分析方法对金属构件进行频谱分析,在0~100Hz范围内找出工件几十种谐波频率,从中优选出效果最佳的5种谐波频率,施加足够的能量进行振动处理,产生多方向动应力,与多维分布的残余应力叠加,达到材料的屈服极限时,将产生局部的塑性变形,如果这种循环的应力幅能迫使某些滑移面上的位错产生滑移或机械孪生,那么尽管没有达到材料的屈服极限,也同样会产生微观的塑性变形,迫使受约束的变形得到释放,从而降低峰值残余应力,达到残余应力均化的目的。频谱谐波时效相比亚共振时效对激振点、支撑点、拾振点的选取无特殊要求,工艺简单,由于振动时效转速在6000r/min以下,振动产生的噪音较低,减小了噪音污染。频谱谐波时效技术在国家节能、减排、环保的背景下,有着广泛应用前景。
2振动过程及结果分析
(1) 频谱谐波时效参数
切割机的底座为大型铸件,其应力消除的好坏将直接影响到上层结构单元的精度。选用北京翔博公司的“领航者消除应力专家系统Window XP版V1.0领航者Ⅱ型”设备进行频谱谐波时效,工件的支撑采用3点减振平稳支撑,激振器通过弓形夹刚性的装夹在底座上,考虑构件的重量和刚度选用了LH3506激振器。在选取时效振型及频率过程中,利用计算机软件控制的灵活性和可操控性,通过频谱谐波模式分析优选出工件5种不同振型的谐波频率进行时效处理,对实验件时效前选择5条测试轨迹进行磁应力检测(如图1),时效后沿着原来检测轨迹再次进行磁应力检测,通过频谱谐波前、后磁应力检测,对比底座应力分布的均化状态。
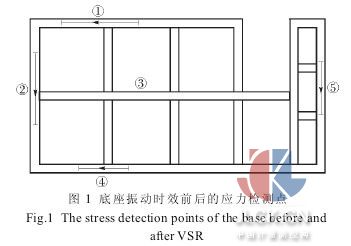
(2) 残余应力测试
为了对频谱谐波时效应力消除效果进行检测,我们在频谱谐波时效前后采用TSC—1M—4型金属磁记忆应力检测仪进行应力检测。金属磁记忆方法的基本原理是金属在残余应力集中区域中产生漏磁场现象, 而漏磁场的变化反映导磁率张量, 这一张量相当于金属在载荷作用下形成的变形或应力张量.通过TSC—1M—4型金属磁记忆应力检测仪对实验工件时效前后漏磁场分布的检测,判断工件内部残余应力分布情况,从而直观地观察时效前后应力消除和均化效果,如图2。频谱谐波时效前后工件梯度峰值下降率见表1。

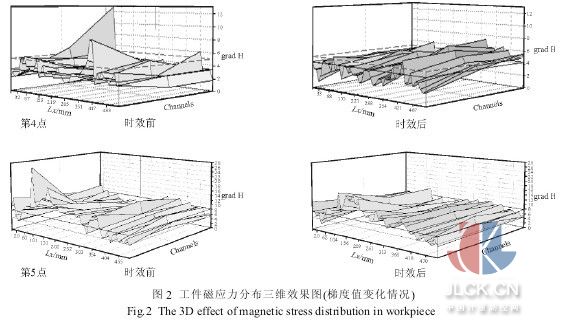
注:X轴表示测试工件轨迹长度,mm;Y轴表示磁场强度梯度变化量(dH/dx表示磁场强度在每毫米的变化量, 单位(A/m)/mm,Z轴表示所测试的通道数。
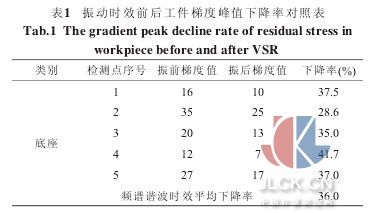
(3) 结果与分析
从图2看到:①时效前磁应力分布不均且存在应力峰值偏高现象,通过时效去应力后峰值应力得到明显下降,残余应力分布趋于均匀; ②通过时效前后梯度值的变化更加直观的说明了峰值应力得到了有效降低,从梯度值下降率来看平均下降率在36%,充分说明了频谱谐波时效残余应力的消除均化效果理想。
采用频谱谐波振动时效对提高生产效率及节约能耗效果也是十分显著的。就底座而言,因为体型过大,自然时效周期太长,而热时效处理从装炉到出炉的退火时间约为3天。退火后产生一定厚度的氧化皮,退火后变形较大,给后期加工带来一定困难。如果采用振动时效的工艺进行处理,底座的处理周期约为1h,而且振动时效不会产生热时效变形,因此底座不存在收缩问题,不存在氧化问题。与热时效相比,采用振动时效进行处理,在消除应力效果显著的同时,还可缩短7天左右的生产工期,并节省大量能源和资金。
4结语
(1) 频谱谐波振动时效处理的底座,由于能够在多个谐波频率施加足够能量进行振动处理,从而在降低峰值残余应力,整体残余应力均匀化方面达到较好处理效果,能够满足设备装配的需要。
(2) 频谱谐波时效技术在稳定构件尺寸精度和消除残余应力方面发挥了很好的作用,该技术在确保质量的前提下能够提高生产效率,降低成本,节能环保,其社会效益和技术经济效益均十分可观。
|